Things to consider before implementing warehouse AMRs
September 30, 2021
Warehouses are transitioning to AMRs (Autonomous Mobile Robots) to replace trolleys, forklifts, conveyor systems and even AGVs (Automated Guided Vehicles). The AMR’s primary role is to improve efficiency and safety in the warehouse space.
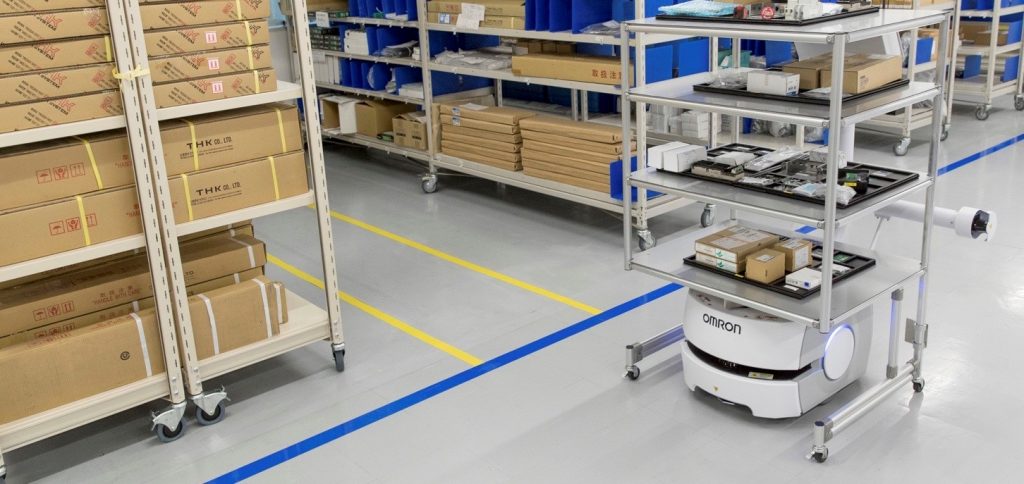
The COVID-19 pandemic is accelerating warehouse automation across the globe.
More warehousing operations are embracing technologies such as traceability, robotics, safety and IIoT.
Warehouses are transitioning to AMRs (Autonomous Mobile Robots) to replace trolleys, forklifts, conveyor systems and even AGVs (Automated Guided Vehicles). The AMR’s primary role is to improve efficiency and safety in the warehouse space.
AMR implementation can be considered a big investment. It can start with a single robot and expand to a total fleet of up to 100 robots. AMRs can operate individually or communicate with WMS (Warehouse Management Systems). Hence, there are many elements to consider.
In the market, people use AMRs and AGVs (Automated Guarded Vehicles) to describe material moving robots. AGVs and AMRs are in fact quite different. Traditionally, AGVs use physical guidance methods such as magnetic tape on the floor. If the path is obstructed, it will stop and wait for the path to be clear before resuming operations. AMRs can navigate the natural features of a facility and require no costly modifications to existing infrastructure. Also, AMRs can work safely alongside humans – usually without interrupting workflow.
Of course, safety is paramount when implementing any new technology. AMRs are becoming bigger, heavier, more complex and even more autonomous. This can create new safety challenges. To tackle these challenges, safety service consultants can provide assistance on mobile robot applications, from the design phase all the way to integration with existing systems.
Due to the larger investments with AMRs, facilities can start with one unit or trial a few units in a test area, for suitability. Once the trial is successful, having reached the targeted throughput, more units can be implemented into the warehouse. Also, with Omron’s latest technology you can now simulate fleets of robots to minimise risks when implementing an AMR project.
The supplier can then provide fleet control – putting all the AMRs under one control – to further improve efficiency and workflow. Proper fleet control/management of mobile robots is essential to ensure they have a central access unit that can control traffic flow in their work environment. This can be more important than comparing specifications on paper, as it dictates the future success of the facility. Hence, choosing the right supplier with a proven history is vital.
Also, it is crucial the AMR system can easily integrate with MES, ERP and WMS systems. The AMR solution provider needs to ensure security complies with the local IT systems. On top of this, traceability can be achieved if scan and check can be done at the same time. Some suppliers, like Omron, can provide both AMR and Traceability solutions together.
Lastly, support service before and after sales is equally important to ensure production levels and efficiency can be maintained. Therefore, local support from the supplier and solution provider is a top tier consideration.
It is vital to ensure the solution you choose incorporates a supplier with local presence of support and engineering with accompanying offices throughout the Oceania region.