The ground-breaking new technology that’s driving logistics to a new level
October 20, 2022
A conveyor system is a fast, efficient way to transport products and materials from one point to another. For many logistics companies, conveyors are the core component of their warehouse operations to streamline production flow.
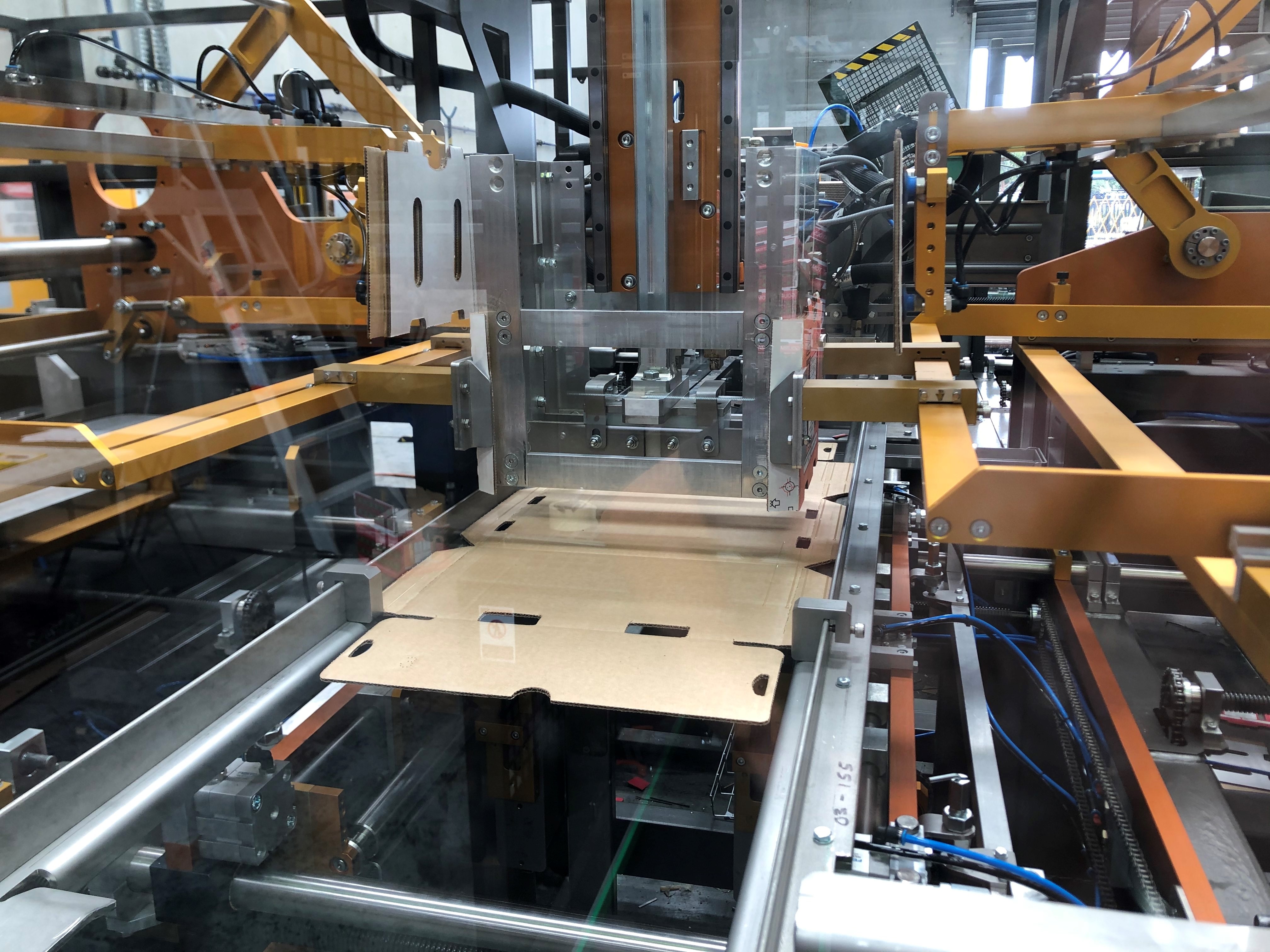
A conveyor system is a fast, efficient way to transport products and materials from one point to another. For many logistics companies, conveyors are the core component of their warehouse operations to streamline production flow.
They can be a “central nervous system” for operations that receive, handle, store, distribute, manufacture or ship products.
Installing the wrong conveyor system can undermine a warehouse’s operational efficiency, leading to higher costs, less throughput and lower customer satisfaction.
A conveyor system operating at maximum efficiency minimises human error, lowers workplace risks and reduces labour costs – among other benefits.
Selecting the right conveyor system for various applications can be a real challenge.
When global logistics giant LF Logistics needed to upgrade its AMR receiving system at a key distribution hub in Melbourne, it turned to Automaint Solutions for the answer.
Automaint Solutions is a Melbourne-based company specialising in automation and special purpose machinery. The company has more than 40 years’ experience in the design, manufacture and installation of turnkey automation systems across a broad range of industries.
The brief was simple. LF Logistics needed 47 custom designed and manufactured AMR delivery pallet conveyor sections for its main distribution centre at Derrimut, an outer Melbourne suburb.
In most cases, conveyors are powered by purpose-built motors and controlled by a processor or Programmable Logic Controller (PLC).
Thinking outside the square.
“But to save costs on this occasion we had to think outside the square,” says Automaint Solutions director Mark Cartwright.
“What the conveyors at LF Logistics do is rather unique. “The system is set up to receive an AMR (automated mobile robot), which in turn drops off pallets onto the moving conveyor.”
To find an effective solution, Automaint partnered with Omron, a preferred supplier of controllers.
“Normally, we would use controllers or PLCs to operate a system of this kind,” said Mr Cartwright.
“But because we are dealing with so many conveyors we had to find a way to write logic directly into the drive system so the conveyor could work independently.”
In collaboration with the experts at Omron, Automaint Solutions were able to set up a system where there was no need for a processor or any other form of controller or PLC.
“This is a real game-changer – and a huge cost saver,” says Mr Cartwright. “Just five years ago we would never have thought to do something as ground-breaking as that.
“It was never considered a preferred method, but it has now proved to be very effective for applications such as this.
“Using Omron equipment we were able to achieve our main goals to automate the entire operation and significantly improve throughput.”
Unique conveyor system
Automaint has already installed all of the 47 conveyors using the new technology – with the first service & inspection due in coming weeks.
“The end result will be a unique conveyor system that can be easily integrated with AMRs to streamline production at the complex,” Mr Cartwright says.
“The biggest benefit has been significant cost savings for all parties involved.”
Going forward, Automaint will consider replicating the new system for similar applications.
“This technology is ideal for conveyor applications where a small amount of I/O is required to control the motor.
“And the benefits for end-users are obvious.
“Rather than having to buy a PLC and install it by wiring it in to I/O or PLC to control the drive, you can do everything directly on the drive using the built-in I/O.
“The software is free to download – so it is a really efficient and cost-effective way to go.”
Mr Cartwright says Automaint has forged a strong working partnership with Omron in recent years that continues to grow.
“We use Omron for all our control systems,” he says.
“Omron remains our preferred supplier for HMIs, servo drives, PLCs, I/O and all integrated control.”