Automaint Solutions delivers a packaging solution that’s outside the box
August 08, 2022
Finding the right solution for the packaging of fresh produce requires a smart mix of speed, precision and flexibility.
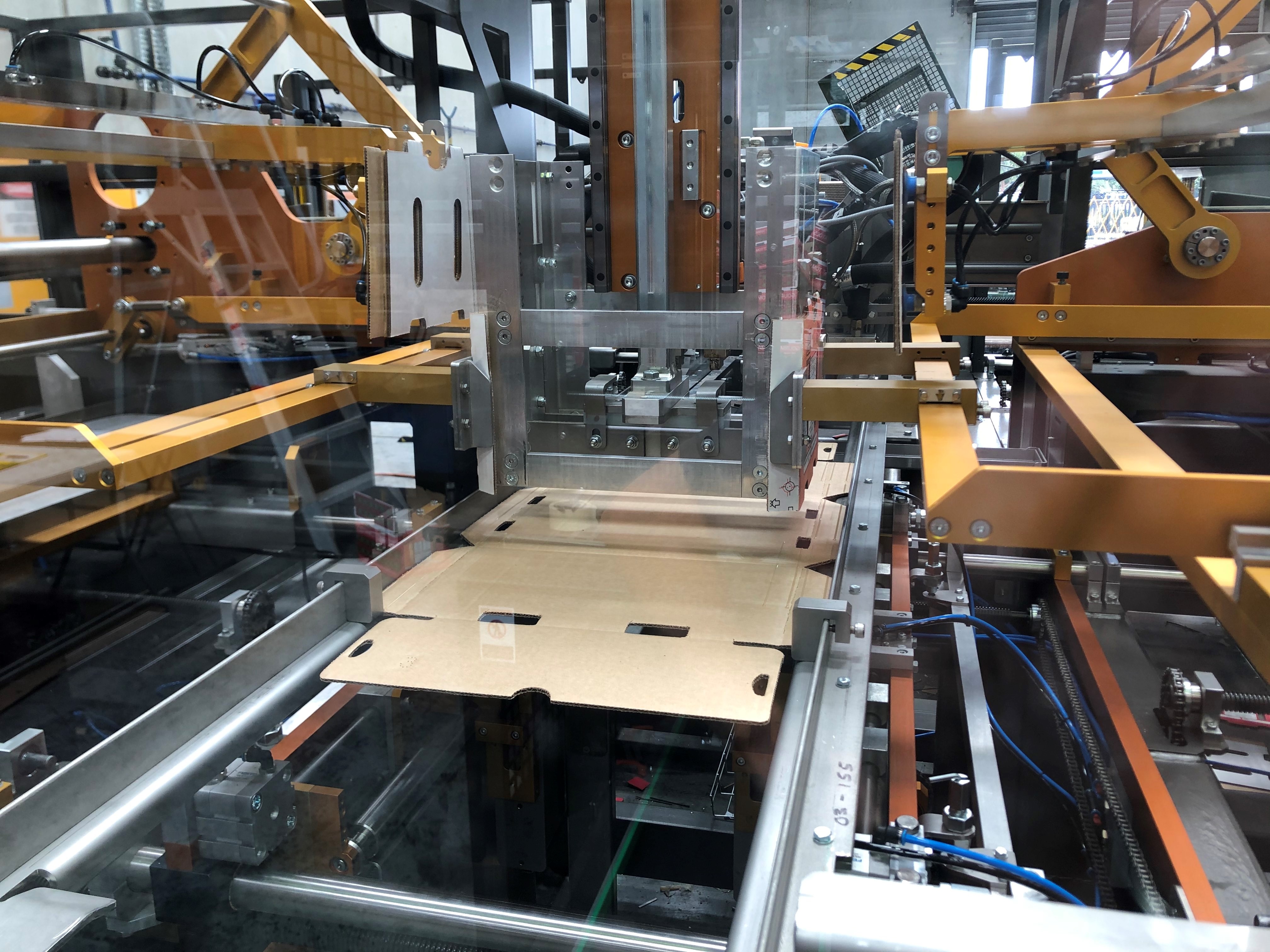
When a leading International packaging company was looking to ramp up production of cardboard boxes for local fruit & vegetable production, it turned to Automaint Solutions for the answer.
Automaint Solutions is a Melbourne-based company, specialising in machinery for the packaging industry. They develop innovative robotics and automation systems to help boost productivity and increase profitability.
“Our customer was looking for a custom- built machine that could produce a range of three-piece box sizes and also stack them at a very fast speed,” explains Automaint Solutions Spokesman, Leighton Markham.
“The aim was to take their business to the next level,” he says. “Previously, they’ve been using separate machines that could produce only 2 or 3 different sizes of cardboard boxes at a fairly slow rate.”
Automaint Solutions developed a new Erector and Stacker that can produce a broad range of sizes with super-fast throughput and simple changeover for the different sizes.
Just one machine is now able to process all available requests at high-speeds – from a small footprint box of 200x200mm, right up to a footprint of 600x600mm.
The erector has all three blanks loaded from the end of the machine, creating an increase in floor space efficiency. Opposition three-piece erectors load from the back and the front of the machine, meaning a lot of moving around the machine to keep it running.
Omron control components drive new system
Automaint Solutions decided their control components would all be Omron – a global leader in industrial automation. To ensure the machine operates at maximum efficiency Omron supplied the following state-of-the-art equipment:
•PLC (NX102 series with SL3300 Safety) – Erector control system
•HMI (NA Series) – Erector user interface
•PLC (CP1L-E Series) – Stacker control system
•HMI (NB Series) – Stacker user interface
•Safety input and output components (including light curtains, door switches and e-stop switches)
•FOUR modular cabinets. (All connected with EtherCAT remote IO Modules).
•Servo systems (1S series) – for motion control to drive actuators for box folding (Nine servos with gear boxes)
•MX2 VSDs – Stacker
•Assorted components including power supplies, relays and push buttons
Mr Markham says the design of the new erector system removes pneumatics where possible, replacing them with servo actions. “This assists in gaining speed,” he says. “It’s also great for customers that have small air supplies on site.”
Also, the stacker is mostly electrical (VSD and AC motors) where possible with minimal pneumatics. Once again this improves efficiency and throughput.Mr Markham says Automaint’s decision to partner with Omron on this project was based on performance and value.
“We have worked with Omron previously and they are a preferred supplier”. “Omron’s Sysmac Studio provides an all-in-one software solution and helps to keep any R&D costs down.“ Also, Omron’s technical assistance is second to none.“ Omron have been a pleasure to deal with on our R&D machines. “The sales and tech team are always happy and always attentive to our needs and the dynamics of our expanding business.”
For more information on this solutions or your would like to speak with sales please contact us.